Autor: Friedrich Dürst
Gibt man den Suchbegriff "5S" in das Eingabefeld von Google ein, so erhält man mehr als 279.000.000 Ergebnisse. Das ist etwa 10 mal soviel wie der Begriff "KAIZEN", 20 mal soviel wie der Begriff "PDCA" und 1.559 mal soviel wie das Ergebnis für "Heijunka". Von daher ist es verwunderlich, dass nur die wenigsten Unternehmen ein halbwegs konkretes Bild davon haben, um was es sich dabei überhaupt handelt. Geht man näher auf die beschriebenen Inhalte ein, so verdichtet sich das Bild, dass 5S oder manchmal auch 5A als das Instrument für "Schöner Wohnen" gilt. "Sicherheit, Ordnung, Sauberkeit" (abk. SOS) wird mit 5S gleichgesetzt und gilt dogmatisch als gleichbedeutend. Somit ist 5S passungsfähig zu der gepflogenen und bekannten tayloristischen Grundhaltungen des Scientific Management, wie sie heute in Unternehmen oder im Militär standardmäßig gelebt wird. Wird dann auch noch die REFA-Methodenlehre kombiniert, ist der Cocktail der Verwirrungen serviert.
Unter dem Deckmantel der "Qualität" wird Mitarbeitern nicht selten suggeriert, dass nur durch das bedingungslose Einhalten des normierten Standards - was immer das auch bedeuten soll - die Grundvorraussetzung für Verbesserung gegeben ist und das Risiko von Arbeitsunfällen sinkt. Die (Selbst-)Disziplinierung endet in einem aus dem Internet heruntergeladenem Auditfragebogen, indem die Bodenmarkierungen und die Positionierung des Abfalleimers zur Erfüllung der Quote in einem täglichen oder wöchentlichen "Go-See" reicht. Mit diesem Menschenbild wären dann auch die Thesen von Douglas McGregor und seiner Theory X (weitere Informationen im Link) aus dem Jahr 1960 bewiesen, erkennbar durch und im Verhalten von objektivierten und demotivierten Mitarbeitern.
Diskutiert man mit selbsternannten oder zertifizierten Experten das Thema, scheinen immer "die Anderen" die Wichtigkeit und Bedeutsamkeit nicht verstanden zu haben. Auf Fragen nach dem "Wozu", dem "Warum" oder auch dem "Wie" werden immer wieder die gleichen, unsinnigen und ignoranten Antworten gegeben. Wieso auch nicht, die Informationen und Powerpoints sind ja alle bedenkenlos voneinander abgeschrieben und kopiert. Es fehlt einfach zu oft die Fähigkeit der Deduktion und die Fertigkeit des systematischen Vorgehens.
Historie von 5S
Versucht man etwas über die Entstehung der 5S herauszufinden, bekommt man unterschiedlichste Quellen genannt. Einige von ihnen bringen gar die Venezianer als Ur-Väter der Methode ins Gespräch. Im Arsenal (arab. "Arbeitsstätte"), der Schiffswerft der ehemaligen Republik Venedig, wurden bereits im 14. Jahrhundert Galeeren in streng rationalisierten Arbeitsabläufen produziert. Diese Werft galt als größter Produktionsbetrieb Europas vor dem Zeitalter der Industrialisierung.
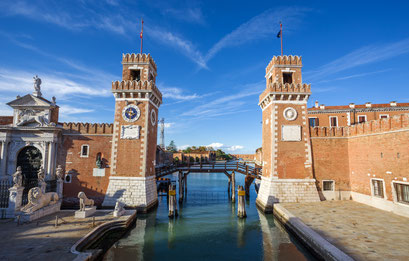
Das Arsenal beinhaltete neben den Schiffsbecken, den Schreinereien, den Kalfateranlagen auch eine lange Seilhalle und sogar Erz- und Gießhütten. Auch ein Pulverlager und ein Waffendepot befand sich auf dem Gelände. Im Zuge des Aufstiegs Venedigs zur Seemacht wurde das Arsenal mehrmals erweitert.
Dabei arbeitete das Arsenal außerordentlich effizient. Die Schiffe waren so konstruiert, dass sie in kürzester Zeit von einem Kriegsschiff in ein Handelsschiff und umgekehrt umgerüstet werden konnten. Alle Bauteile hierzu waren genormt und lagen vorgefertigt im Depot. Im Krieg gegen das Osmanische Reich konnten so im Jahr 1571 für die Seeschlacht von Lepanto 100 Galeeren in nur 14 Tagen umgebaut werden.
Für diese Effektivität und Effizienz war eine durchdachte Organisation notwendig. Um möglichst schnell Entscheidungswege zu gewährleisten, waren die obersten Leiter des Arsenals stets für eine befristete Zeit gewählte Mitglieder des Großen Rates. Die Handwerker, Schiffszimmerleute, Pecher, Mastenkonstrukteure, Segelmacher, Schmiede, Gießereiarbeiter und sonstigen Arbeiter waren in sich selbstorganisierenden Kleingruppen strukturiert und arbeiteten gewöhnlich unter Meistern als eine Art Subunternehmer. Dazu waren sie sehr angesehen, wurden beachtlich entlohnt und genossen eine Reihe von Privilegien, um ein Abwandern zur Konkurrenz zu verhindern. Des Weiteren wurde den Arbeitern kostenloser Wohnraum zur Verfügung gestellt.
Das Arsenal kann man heute noch in Venedig besichtigen, jedoch ist von der damaligen industriellen Fertigung nichts mehr vorhanden.
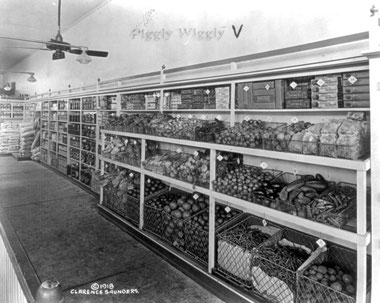
Andere Quellen berichten von den Gründern von Toyota als Erfinder der 5S-Philosophie. Sakichi Toyoda, sein Sohn Kiichiro und Taiichi Ohno, der Chefingenieur des Unternehmens, besuchten mehrere US-Unternehmen, darunter die Ford Motor Company und die Supermarktkette Piggly Wiggly. Die drei Vertreter von Toyota untersuchten sowohl die Montagelinien bei Ford, als auch den Nachschubprozess bei der Supermarktkette. In ihren Beobachtungen bemerkten sie, dass Arbeiter bei Ford immer warten mussten, bis ein Schritt abgeschlossen war, was zu Entlassungen und Neueinstellungen führte. In den Supermärkten von Piggly Wiggly half ihnen das Inventarsystem den Just-In-Time-Prozess zu verstehen, indem nur das nachbestellt wurde, was auch verkauft wurde. Angeblich war dieser Sachverhalt für Taiichi Ohno die Initialzündung, den Zustand des Jit zu verstehen und in die 5S-Methodik zu integrieren. Unabhängig der Richtigkeit dieser Quelle bot die 5S-Methodik jedem Mitarbeiter bei Toyota ein Maß an Wichtigkeit und Ermutigung, dass jeder Job für den Prozess und das Endprodukt wesentlich war. Muda wurde so auf ein Minimum reduziert und die Organisation des Arbeitsbereichs führte zu zeitnahen Ergebnissen mit echt stolzen Mitarbeiter.
Der Begriff 5S taucht tatsächlich erst in den späten 1980er Jahren auf. Sehr oft werden damit zwei Namen in Verbindung gebracht, und zwar der von Takashi Osada, ehemaliger Toyota-Chef, und Hiroyuki Hirano, Ingenieur und Jit-Experte. Beide Japaner beschäftigten sich intensiv mit einem Gesamtansatz für Produktionssysteme, die eine Just-in-time-Fertigkeit eines Unternehmens anstreben.
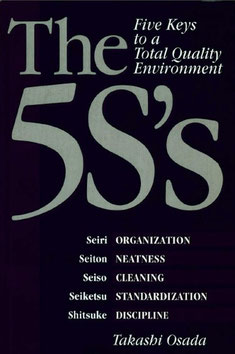
Einen Rahmen für die Anwendung von 5S in Unternehmen (im Sinne einer persönlichen Lebensphilosophie) wurde erstmals in den frühen 1980er Jahren von Takashi Osada in seinem Buch "The 5S's: Five Keys to a Total Quality Environment" formalisiert. Laut Osada zielt die Praxis von 5S darauf ab, die Werte "Organisation, Sauberkeit, Reinigung, Standardisierung und Disziplin" in den Arbeitsplatz einzubetten. Das Verständnis von 5S ist in Japan detailliert und tief verwurzelt, da es aus einem Ansatz stammt, der es als Lebensweisheit betrachtet, die jeden Tag praktiziert wird. So wurde 5S in Japan ziemlich schnell im verarbeitenden Gewerbe eingeführt und auf andere Branchen und Dienstleistungssektoren ausgeweitet. Ein entscheidender Punkt in Osadas Werk ist es, dass die Implementierung von 5S versteckte Probleme aufdeckt, die ansonsten möglicherweise unbemerkt bleiben. Zusammengefasst beschreibt er folgende Vorteile:
- Seiri und Seiton - Maximierung der Effizienz und Effektivität durch Reduzierung der Arbeitsbelastung, menschlicher Fehler durch Vereinfachung der Prozesse.
- Seiso und Seiketsu - Maximierung der Wirksamkeit durch Beitrag zu einem gesünderen Leben, Sicherheit und Wohlbefinden sowie Verbesserung der Transparenz.
- Shitsuke - durch Aus- und Weiterbildung zur Verbesserung der Moral, was zu einer Verbesserung der Qualität von Arbeit / Leben und Arbeitsstandards führt.
Innerhalb Japans wird versucht, die Praxis von 5S mit anderen japanischen Lebensweisheiten, Kaizen (Veränderung zum Besseren) und Me-de-Miru-Methode (Visuell-Control) zu kombinieren. Dieses integrierte System des Denkens und Managements wird zu Me-de-Miru Kanri, einem visuellen Kontrollsystem vereint. Damit werden die ersten 3S (Seiri, Seiton und Seiso) des 5S-Konzepts stärker betont. Angesichts der Tatsache, dass dies ausserhalb Japans recht unbeachtet und unerforscht blieb, hat es zu einer vereinfachten englischen Übersetzung von 5S als „houskeeping" (Ordnung und Sauberkeit) geführt.
Haben jedoch alle Mitglieder einer Organisation 5S vollständig verstanden und ist es implementiert, wird die organisatorische Bereitschaft zur Best Practice realistischer, da eines der Ergebnisse erfolgreicher 5S-Praktiken eine erhöhte Moral und organisatorische Belastbarkeit ist, so Osada.
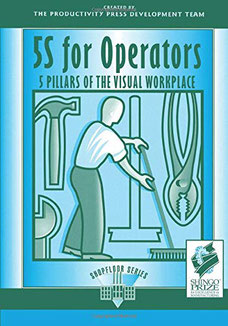
Ursprünglich war das Toyota-Produktionssystem ein streng gehütetes Geheimnis. Aber der massive wirtschaftliche Aufschwung Japans in den 1980er Jahren erregte großes Interesse bei ausländischen Unternehmen, die sich fragten, wie Toyota so viele Produkte bauen konnte, auf so hohem Qualitätsniveau. Als ein allmählicher internationaler Gedankenaustausch Gestalt annahm, entwarf der Autor und Geschäftsführer von ULVAC Inc., Hiroyuki Hirano, die "5 Pillars of the Visual Workplace", ein Konzept, das sich in die heutige 5S-Methodik verwandeln würde. 5S wurde von Hiroyuki Hirano im Rahmen seines Gesamtansatzes für Produktionssysteme entwickelt. Hirano bot jedoch eine Struktur für ein Verbesserungsprogramm an, ausdrücklich nicht für "housekeeping". Er wies auf eine Reihe identifizierbarer Schritte hin, die jeweils auf ihrem Vorgänger aufbauen. Im Mittelpunkt steht das Prinzip, dass für den Prozess nicht wesentliche Elemente entfernt - an anderer Stelle gelagert oder vollständig entfernt werden sollten. Durch die Unterscheidung zwischen Seiri und Seiton machte Hirano diesen Sachverhalt deutlich. Ebenso beschreibt er die Seiso-Phase als ein eigenständiges Element. Hirano ist der Ansicht, dass die Definition einer Reinigungsmethode (Seiso) eine diskrete Aktivität ist, die nicht mit der Organisation und Struktur des Arbeitsablaufes zu verwechseln ist. Hirano erinnerte die Welt auch an den Hawthorne-Effekt. In den Methodenlehren von Soziologie und Psychologie versteht man darunter den Effekt, dass Versuchspersonen ihr natürliches Verhalten ändern können, wenn sie wissen, dass sie Teilnehmer an einer Untersuchung sind (Artefakt). Es kann also sein, dass die Ergebnisse einer Studie durch die Studie selbst verfälscht werden. Im Extremfall ist der beobachtete Effekt vollständig durch die Studiensituation selbst entstanden. Möglicherweise haben deswegen insbesondere westliche Manager von der Unterscheidung zwischen den Seiketsu und Shitsuke profitiert.
Diese beiden Bücher fassten die 5S-Methode auf eine Weise zusammen, die für Unternehmen außerhalb Japans leicht zu befolgen war, jedes mit einem etwas anderen Schwerpunkt. Hiranos Buch verfolgte einen praktischen Ansatz. Osadas Buch war konzeptioneller und beinhaltete eine stärkere Diskussion der Managementphilosophie. Während beide betonten, wie wichtig es ist, visuelle Hinweise am Arbeitsplatz zu haben, setzte Hirano den Begriff „visueller Arbeitsplatz“ in den Titel seines Buches ein.
Als Werkzeug hatte 5S neben dem gesunden Menschenverstand, dass ein übersichtlicher Arbeitsplatz effizienter ist, zwei weitere Vorteile. Erstens war die 5S-Methode leicht zu verstehend, zweitens relativ kostengünstig einzuführen.
Allgemeines Verständnis von 5S
Die Grundgedanken des 5S hatten sich zu einer Zeit entwickelt, in der Unternehmen vor beherrschbaren Rahmenbedingungen standen. Dabei war die Variantenanzahl überschaubar, die Märkte und die Bedarfe nicht erschlossen und vor allem nicht gesättigt und die Konkurrenz schien keine Gefahr. Wachstum war folglich ein kleines Problem, denn die Umwelt bestrafte die eigene Unfähigkeit nur selten. Viele Unternehmen wagten den Schritt von der Manufaktur oder dem Handwerk in industrielle Strukturen.
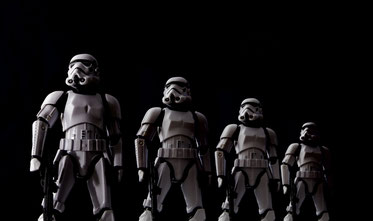
Wo der protestantische und kalvinistische Norden schon im frühen 20. Jahrhundert massenhaft Produkte mir annehmbarer Funktionalität herstellten, industrialisiert die vornehmlich katholische Süden manchmal erst nach dem 2. Weltkrieg (siehe auch hier). Im ersten Zeitalter der Maschinen war das Ansinnen, Unternehmen und Organisationen genau wie solche triviale Maschinen zu errichten und zu betreiben. Mit diesem Verständnis setzten viele Unternehmen weltweit folglich auch den Ansatz des 5S ein. Welches Unternehmen ausserhalb Japans kann schon was mir den Begriffen "Monozukuri" oder "Hansei" anfangen, geschweige denn die dahinter liegende Kultur verstehen? Das militärische Narrativ des "Command and Control" war dagegen schon sehr früh in Unternehmen eingezogen, und sie war so viel einfacher.
Nachdem jedoch, scheinbar unbemerkt, die Vernetzung des Materialflusses durch weltweite Logistik und die Vernetzung des Informationsflusses durch das World Wide Web die so beherrschbaren Rahmenbedingungen auf den Kopf stellte, war man auf der Suche nach neuen effizienzsteigernden Heilsbringern. Berauscht und geblendet von der inneren Haltung, dass jegliche Aktion zu einem "Mehr" führt, stockten erstmals die Wirkungen von ach so tollen Optimierungsprojekten.
Als dann die Welle der "Lean-Production" in der Mitte der 90er Jahre des letzten Jahrhunderts in die Unternehmen des Abendlandes ankamen, schien der banale Werkzeugkasten gleich mitgeliefert. Die erste Literatur berichtete von simplen Werkzeugen, die nur durch Anwenden in den Erfolg führten. Die Frage war nur, wie implementiert man diese Werkzeuge in die vorhandenen Strukturen der tayloristischen Unternehmen? Im Fall des 5S war das sehr einfach. Mittels der direkten Übersetzung der japanischen Worte bestätigte man das vorhandene Unternehmensmodell. Wie überall zu lesen bedeuten die gedeuteten Einzelbegriffe folgendes (Quelle Wikipedia):
- SEIRI: Sortiere aus. Alles was für die Arbeit an diesem Platz nicht benötigt wird, wird aussortiert.
- SEITON: Stelle ordentlich hin. Was tatsächlich gebraucht wird, bekommt einen unter ergonomischen Gesichtspunkten ausgesuchten, definierten und gekennzeichneten festen Platz.
- SEISO: Säubere. Jeder reinigt seinen Arbeitsplatz und seine Arbeitsutensilien selbst. Dabei werden Mängel erkannt, markiert und stetig abgearbeitet. Die Reinigung dient dem Prüfen.
- SEIKETSU: Standardisiere. Das bedeutet Verwendung von einheitlichen Kennzeichnungen, Beschriftungen und Markierungen am gesamten Arbeitsplatz zu jeder Zeit. Stetiges Aufräumen verhindert, dass neue Gegenstände ungeplanten Zugang zum Arbeitsplatz finden.
- SHITSUKE: Selbstdisziplin und ständige Verbesserung. Damit Ordnung und Sauberkeit aufrechterhalten werden, ist Disziplin erforderlich. Ist eine Stellfläche für ein Werkzeug definiert, gehört es auch immer dahin. Es werden regelmäßige Kontrollen durchgeführt und Abweichungen notiert. Festgestellte Abweichungen müssen beseitigt werden.
Oft werden die fünf Begriffe erweitert mit beispielsweise "Sicherheit" oder ähnlichem. Wer nun glaubt, im heutigen Umfeld mit diesen fünf Begriffen und der dahinter liegenden konditionierten tayloristischen Geisteshaltung eine konkrete Wirkung für Kunde, Mitarbeiter, Produkt oder Prozess im aktuellen high-mix-low-volume Umfeld zu erzeugen, dem kann nur bedingt geholfen werden.
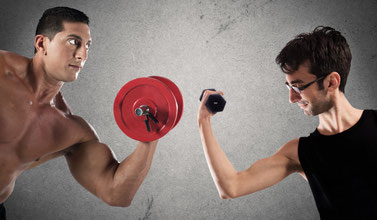
Diese Formulierung und Interpretation der 5S lässt nämlich gar keine Veränderung zu, denn es wird im besten Fall der bestehende Zustand verwaltet. Das betrachtete System wird zur Arbeitsnorm. Die Krönung ist die Objektivierung mittels einer Kennzahl und einer KPI-Spinne, die mit einem Auditfragebogen erhoben und in der monatlichen Durchsprachen auf Abteilungsleiterebene verglichen wird.
Die hoch-komplizierten Systeme, zu denen unsere Produktionen durch den Paradigmenwechsel geworden sind, werden durch diese Trivialisierung und Normierung noch handlungsunfähiger. Weiter widerspricht jegliche Eigenoptimierung der Mitarbeiter des Arbeitssystems der Norm, und wenn sie gehört wird, dann meist in der jährlichen 5S-Kampagne. Schliesslich zählt ausserhalb von Toyota eine tägliche Optimierung ja nicht als Arbeit, sondern reduziert die Effizienz. Das ist aber nicht der Grundgedanke von Kaizen! Es wird Zeit für eine neue Interpretation.
Die "neuen 5S"
Um sich im 21. Jahrhundert den anstehenden Herausforderungen zu stellen, sollte man sich der vorherrschenden Bedingungen bewusst werden. Die Welt ist im Material- und Informationsfluss nahezu vollständig erschlossen, großes Wachstum mit einfachen Ideen ist nur noch in Ausnahmezufällen möglich und die Märkte sind nicht nur gesättigt, sie sind übersättigt. Wir haben mehr als wir benötigen, vernichten in den Industrieländern bis zu 50% aller erzeugten Nahrungsmitteln. Seit Amazon und Netflix ist "heute bestellt, morgen geliefert" und "Video-on-Demand" als Basismerkmal fest in unserem Leben verankert. Jegliche Information steht nicht nur bei Wikipedia 24/7 zur Verfügung. Ein Problem mit Effizienzen ("So viel wie möglich") haben wir nicht mehr, denn mehr "vom Gleichen" können unsere Hochleistungsmaschinen problemlos erzeugen. Wenn Unternehmen noch wachsen, dann meist in Innovation und damit in Varianz. Die Anzahl der Unternehmen, die sich wirklich noch mit fundierter Grundlagenforschung beschäftigen und damit erfolgreich sind, ist an einer Hand abzuzählen.
Das Schlagwort der heutigen Zeit ist nicht mehr die ökonomische Effizienz, sondern die ökologische Effektivität ("So gut wie möglich"). Hierbei bezieht sich das Adjektiv "gut" auf die Erfüllung des angestrebten Ergebnisses. Das kann alles sein, von Verkaufspreis, bis zu Lieferzeit, Design und auch individuelle technische Problemlösung. Um dies zu gewährleisten, muss in Unternehmen eine Fähigkeit und eine Fertigkeit erzeugt werden, die es ermöglich, diese Art von Ergebnissen anzupeilen. Das Ziel ist folglich, aus einem stabilen Zustand (Exploitation) - durch eine krisenhafte Störung (Exploration) - in einen neuen stabilen Zustand zu wachsen. Diese Fähigkeit von Organisationen, gleichzeitig effektiv und flexibel zu sein, nennt man unter organisationale Ambidextrie. Dabei sollte dieser neue Zustand immer etwas mit dem Suchhorizont des Leistungs- oder Nutzenempfängers zu tun haben. Die jeweilige Stabilität ist notwendig, um handlungs-und wirkungsfähig zu sein. In der Störung ist das Unternehmen (vgl. sozio-technische-System) leicht anfällig, jedoch liegt nur in diesem unternehmerischen Prozessmusterwechsel der Mehrwert (vgl. Wertschöpfung) für Kunden und Unternehmen.
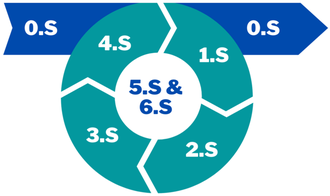
Im Rahmen dieses Prozessmusterwechsels (Mensch durch Kaizen, Prozess durch Kairyo) nimmt der Erkenntnisweg des 5S die erste entscheidende Rolle ein. 5S ist der entscheidende Ordnungsrahmen, der in der nächste Stabilität mündet. Ist das System stabil (d.h. es lebt ohne äussere Einwirkung auf einem konstanten Niveau), muss erst wieder ein "großer Schritt" (krisenhafte Störung) erfolgen, bevor die nächste Stabilisierungsphase beginnen kann. Damit hat jede Stabilisierungsphase ein Ende, und zwar die Stabilität. Technische Systeme habe unter konstanten Bedingungen meist ein bestimmtes maximales Niveau, dass natürlich oder physikalisch erreicht werden kann.
Wann und wie hoch der Fortschritt ausfällt, ist weder terminierbar noch vorhersagbar. Denn betroffene Menschen in einem sozio-technischen System entscheiden selbst, wann und wie sie ein neues Muster annehmen, und nicht der Vorgesetzte oder der Projektplan. Somit wird und ist 5S unumgänglichen Tagesgeschäft und bedingt auch einer geeigneten Form der kooperativen Führung. Alleine Vorgesetzter zu sein ist da ungenügend. Schliesslich darf der sozial-emotionale, wie auch der sachlich-rationale Aspekt aller Beteiligter an der Veränderung nicht aus den Augen verloren werden.
Grundsätzlich sollte bei de Anwendung jeglicher Methode zuerst das Problem erörtert werden, denn die angewendete Methode sollte immer zum Problem passen. Als zweites sollte man sich im Klaren sein, ob man ausreichende Erfahrungen und Kompetenzen in und mit der gewählten Methode vereint. Und schliesslich sollte man auch Gewissheit darüber haben, ob man wirklich an einem Taktgeber (oder Engpass) arbeitet, alles andere wäre Zeit- und Geldverschwendung.
Ist man soweit, kann die Stabilisierung beginnen. Die "neuen 5S" haben wie die ursprünglichen auch eine systematische Reihenfolge und bauen aufeinander auf. Ein Überspringen führt in die Sackgasse. Wie auch im Fall von Hirano wurden die einzelnen "S" weiter zerteilt, um eine Eindeutigkeit und Klarheit herauszustellen. Weiter ist es auch vollkommen nebensächlich, ob es sich um einen Prozess aus Produktion, Administration oder sonstigem Businesskontext handelt.
0.S: Sachverhalt klären, Situation verstehen
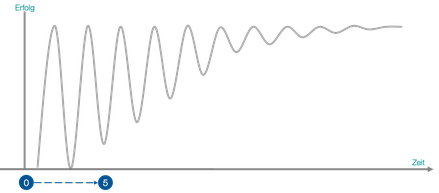
Bevor irgendeine Tätigkeit oder Maßnahme angestoßen wird, muss immer erst geklärt werden, wie sich die Ist-Situation darstellt. Die Herausforderung ist dabei, das "Wozu" und "Warum" herauszustellen und zu verdeutlichen. Findet keine Sinnkoppelung mit den Beteiligten statt, ist die Wahrscheinlichkeit gering, dass irgendeine Wirkung entstehen wird. Die Gefahr ist sogar groß, dass man ins alte Muster zurückfällt oder erst gar nicht beginnt. Deswegen sollte immer das "what´s in for me" für alle Beteiligten beantwortet werden. Eine "Strategische Entscheidung" oder ein "Markt verlangt" ist kein ausreichender Grund. Und natürlich sollte/n auch immer der/die die Stabilisierung durchführen, der/die dafür am besten geeignet ist/sind. Nützlich Fragen dazu sind folgende:
Dieser Punkt sollte mit allen diskutiert werden, denn ohne Bedeutsamkeit wird kein emotionaler Antrieb, und damit keine Selbstdisziplin entstehen (vgl. "5.S"). Fällt man später ins alte Muster zurück, hat man meist hier schon etwas vergessen.
Als Hilfsmittel/Werkzeuge dienen hier dezidierte Prozessanalysen wie die PQPR. Die klassische Wertstromanalyse macht hier keinen Sinn, denn diese ist nur für lineare Ketten (ohne Zeitspreizungen/kreuzende Materialflüsse) der Massenfertigung geeignet.
1.S: Sortiere aus
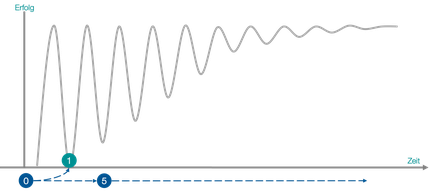
Dieser Punkt zielt auf das Ergebnis, dass alles für eine Stabilisierung vorbereitet ist. Hierzu muss man sich auf das Problem und den Prozess fokussiere und konzentrieren.
Alle Dinge, die nicht dazu gehören werden entfernt, defekte Utenslien werden ersetzt oder repariert. Notwendige Dinge werden besorgt. Alle Werkzeuge und Hilfsmittel funktionieren tadellos.
Eine "Rote-Karten-Aktion" ist meist nicht nötig, wenn das "0.S" gewissenhaft bestimmt ist. Der Gefahr der Ablenkung von Randproblemen sollen durch die Fokussierung gering ausfallen. Ggf. wird hier eine Grundreinigung gemacht.
2.S: Systematisieren, Standard bestimmen
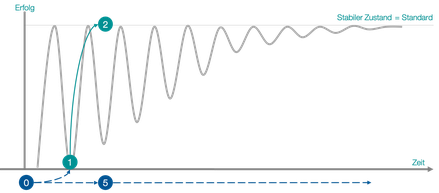
In diesem Schritt ist Erfahrung und Hirnleistung gefragt. Denn aus Produktsicht wird die optimale Reihenfolge der Vorgangskette entwickelt. Dabei ist es nicht von Bedeutung, ob es Hindernisse gibt. Diese werden hier vernachlässigt, man will ja die ideale oder beste Reihenfolge der Vorgangskette designen. Interessant ist es, was wirklich im Prozess erreicht werden kann, man geht an das absolute Maximum.
Man wiederholt den Prozess so oft, bis er flüssig abläuft. Manchmal ist es hilfreich, das fertige Produkt oder die erstellte Dienstleistung rückwärts zu zerlegen, um eine geeignete Reihenfolge zu definieren. Der Fokus liegt immer auf: erst Prozess, dann Werkzeug, dann Material. Dannach wird der Aufwand für jeden Vorgang ermittelt und ggf. das geeignete Linienbetriebsmodell bestimmt. Der zu erreichende Wert für den Aufwand wird in den seltensten Fällen von den Beteiligten angezweifelt, schliesslich habe sie ihn ja ermittelt.
Diese optimale Vorgangskette ist der sogenannte Standard. Damit ist der Standard nie etwas "altes", sondern immer eine anzustrebende Richtung. Die Dokumente, die den Standard abbilden, sind das Standard-Arbeits-Blatt (Download SAB) und das Arbeite-Verteilungs-Blatt (Download AVB).
3.S: Sichtbar machen
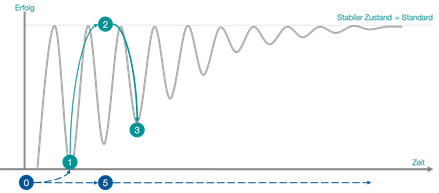
Ist der Standard definiert, geht es darum, alles aufzuzeigen, was den Prozess hindert, im Standard betrieben werden zu können. Diese Hindernisse werden oft auch als Fehlerbilder bezeichnet, da die Ursache meist (noch) nicht eindeutig bekannt ist. Der Ordnungsrahmen in diesem Schritt ist das sogenannte Genba-Kanri, oft lapidar mit Shopfloor-Mamangent übersetzt. Dazu wird am Taktgeber stündlich (oder einem anderen geeigneten Intervall) der Durchsatz an Gutteilen gemessen und notiert. Das für die Abweichung von der Planmenge verantwortliche Fehlerbild wird ebenfalls notiert, und in eine Verlustzeit umgerechnet. Damit hat man für jedes Fehlerbild eine Wertigkeit bestimmt. Das verwendete Dokument ist das "Taktgeberprotokoll" (Download TGP). Am Ende der Schicht werden die Werte des Taktgeberprotokolls auf die entsprechenden Vorlagen "Fehlerbildübersicht" (Download FBÜ) und "Durchsatzprotokoll" (Download DSP) übertragen. Nach einigen Tagen/Wochen bekommt man eine sehr gute Übersicht über Schwachstellen und Fehlerbildhäufungen. Die Bewertung in Verlustzeiten (vgl. OEE) zeigt die größten Zeit- und Kostentreiber. Diese sind für alle sichtbar und können in der täglichen Genba-Runde präsentiert werden.
4.S: Stabilisieren bis zum Standard
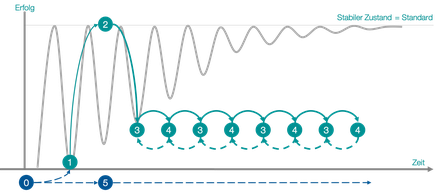
Im 4.S werden die Hindernisse, die im 3.S detektiet wurden, aus dem Weg geräumt. Dazu wird im Team "ein" Fehlerbild ausgewählt. Oft ist es das, das die als Summe die größte Verlustzeit bedingt. In einem zweiten Schritt wird die Person oder das Team benannt, dass die höchste Kompetenz für diese Problemlösung innehat. Natürlich benötigen die Problemlöser freie Kapazitäten, so nebenbei ist noch kein Problem gelöst worden. Für die Suche nach der Problemursache bewährt sich die Vorgehensweise der 5Why und ggf. der A3-Report (PDCA/PDSA). Sind die Ursachen der zu lösenden Probleme offensichtlich oder eindeutig, kann auf die strukturierte Vorgehensweise des A3 verzichtet werden. Ist eine Ursache gefunden und eine Maßnahme durchgeführt, beobachtet man an der Fehlerbildübersicht die Wirksamkeit der Maßnahme. Taucht das Fehlerbild erneut auf, ist man auf der Ursachensuche irgendwo falsch abgebogen. Bei der Bearbeitung des A3-Reports orientiert man sich am 3G-Prinzip: Genba, Genbutsu, Genjitsu. Ein Problemlösung mit Ishikawa im Büro oder Meetingraum ohne 3G ist fahrlässig. Mehr dazu in einem eigenen Beitrag.
Ist das Problem gelöst (Fehlerbild taucht nicht mehr auf und Durchsatz erhöht sich), kann aus der Fehlerbildübersicht das nächste Hindernisse ausgewählt werden. Diese kurzzyklische Iteration zwischen 3.S und 4.S wird auch oft als "kontinuierliche Prozessverbesserung" (vgl. continuous improvement) bezeichnet. Oft wird fälschlicherweise der Begriff "Kaizen" in diesem Zusammenhang genannt. Richtigerweise spricht man hier von Kairyo.
5.S und 6.S: Selbstdisziplin und Selbstgewöhnung
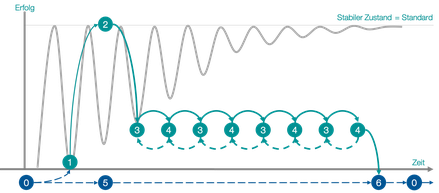
Diese kurzzyklischen Iterationen zwischen 3.S und 4.S werden solange wiederholt, bis alle gravierende Fehlerbilder verschwunden sind. Dabei sollte ein Zyklus maximal 7-10 Tage dauern.
Der innere Antrieb, der einen Problemlöser immer wieder in die Problemlösung treibt, ist das 5.S, die Selbstdisziplin. Ohne eine bestimmte Bedeutsamkeit und auch erlangten Erfolg, wird dieser emotionale Antrieb schwinden. Aus diesem Grund ist das 5.S direkt mit dem 0.S verknüpft, denn hier muss die Bedeutsamkeit und der Nutzen für jeden Beteiligten bewusst werden.
Die Optimierung von technischen Systemen ist meist sehr schnell und schnell stabil. Menschen jedoch tun sich oft schwer mit Veränderungen. Damit neue Verhaltensmuster stabil auf einem Niveau verbleiben, ist Training und Betreuung unumgänglich. Objektivierung, Kontrolle, extrinsische Motivation oder gar Angsterzeugung haben hier rein gar nichts zu suchen. Diskussion, Selbstreflexion, Lernen und Probieren sind hier die besseren Ratgeber. Und Erfolge müssen letztendlich auch gefeiert und belohnt werden. Google doch mal den Begriff "Nomikai"! (link)
Ist das System stabil, d.h. es verharrt auf einem bestimmten Niveau, oder es kehrt nach einer Störung dahin wieder zurück, kann ein neuer Standard angepeilt werden. Ob das noch der selbe Prozess, oder ein anderer ist, hängt immer von den sich ändernden Rahmenbedingungen ab, schliesslich ändern sich die Anforderungen an Organisationen von Zeit zu Zeit.
Fazit
Hat man sich dazu entschieden, in kleinen und großen Schritten seine Maschinen, Arbeitsplätze, Prozesse und Probleme in den Griff zu bekommen, dann geht kein Weg an 5S vorbei. Mit den "neuen 5S" ist ein System und Ordnungsrahmen formuliert, der innerhalb dieses Ordnungsrahmens einen Weg in die organisationale Ambidextrie oder die lernende Organisation aufzeigt. 5S ist kein triviales Werkzeug, und auch nicht das Synonym für Ordnung und Sauberkeit, sondern ein Erkenntnisweg für Bedeutsamkeit, Handlungsfähigkeit und Struktur. Und vor allem ist 5S ein entscheidender Teil auf dem Weg zu Just-in-time. In Verbindung mir Heijunka entfaltet es seine gesamte Power.
Untersucht man die allgemein bekannten und beschriebenen Lean-Methoden detaillierter, wird man schnell herausfinden, dass diese nur eine Abklatsch der Anwendung von 5S sind, denn Value-Stream-Mapping oder auch SMED sind nichts anderes als 5S in einem anderem Gewand.
Sowohl die Stabilisierung ("kleiner Schritt"), als auch der Prozessmusterwechsel ("großer Schritt") benötigt Führung mit Prinzipien, Paradigmen und temporär geltenden Dikta. Menschen müssen nämlich in die Autonomie geführt werden, wenn sie Jahrzehnte lang auf allen hierarchischen Ebenen zu Befehlsempfängern konditioniert wurden. Ohne diese emotionale Pertubation wird kein Lernen gelingen. Übernimmt die Gruppe selbst die Führung und auch die Verantwortung für sich und andere, kann eine Selbstorganisation funktionieren.
Ändern sich die Anforderungen an die Umwelt des Ordnungsrahmens, muss das System in eine neue Stabilität geführt werden, bleiben die Rahmen- oder Umweltbedingungen konstant, kann der Ordnungsrahmen erweitert werden.
Literaturempfehlung, Quellen und Bildnachweis
Osada, Takashi:
The 5S's: Five Keys to a Total Quality Environment (link),
Auflage 1, Tokio, Asian Productivity Organization, 1991 (ISBN-10 9283311159, ISBN-13 978-9283311159)
Hirano, Hiroyuki.:
5S for Operators: 5 Pillars of the Visual Workplace (link),
Auflage 1, London, Taylor & Francis Group, 1996 (ISBN-10 9781563271236, ISBN-13 978-9781563271236)
Hüther, Gerald:
Was wir sein können. Führen in Gemeinschaften (link),
https://www.youtube.com/watch?v=uhSbULHywRg
Bildnachweis: Foto Vorschau: "© phoderstock – stock.adobe.com.", Foto Text: "© phant – stock.adobe.com.", "© Willrow Hood – stock.adobe.com.", "© alphaspirit – stock.adobe.com.", "© dht-Consulting&Management UG"
Kommentar schreiben